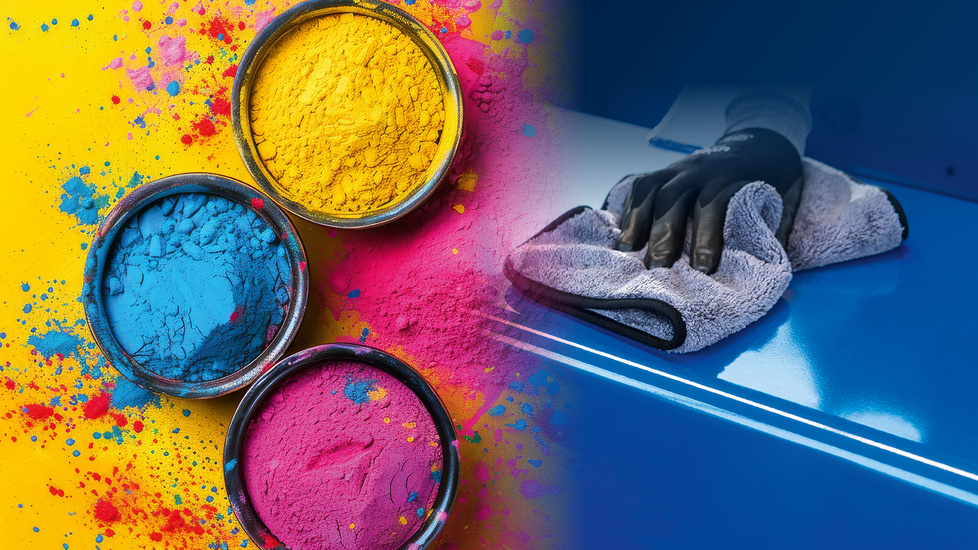
surface center
We for more environmental protection
Perfect surface coating for maximum protection against corrosion: Our surface center (OFZ) in Werlte is the heart of our KRONE quality offensive. This is where our chassis are dip-coated and powder-coated for you in almost fully automated systems.
The coating facility is located in a hall measuring 120 by 130 meters and up to 20.5 meters high. 16,500 square meters offer enough space for the surface center with an integrated, fully automated chassis warehouse. The goal: the highest quality to provide you with the best vehicles for the challenges of your business.
The KRONE surface centre
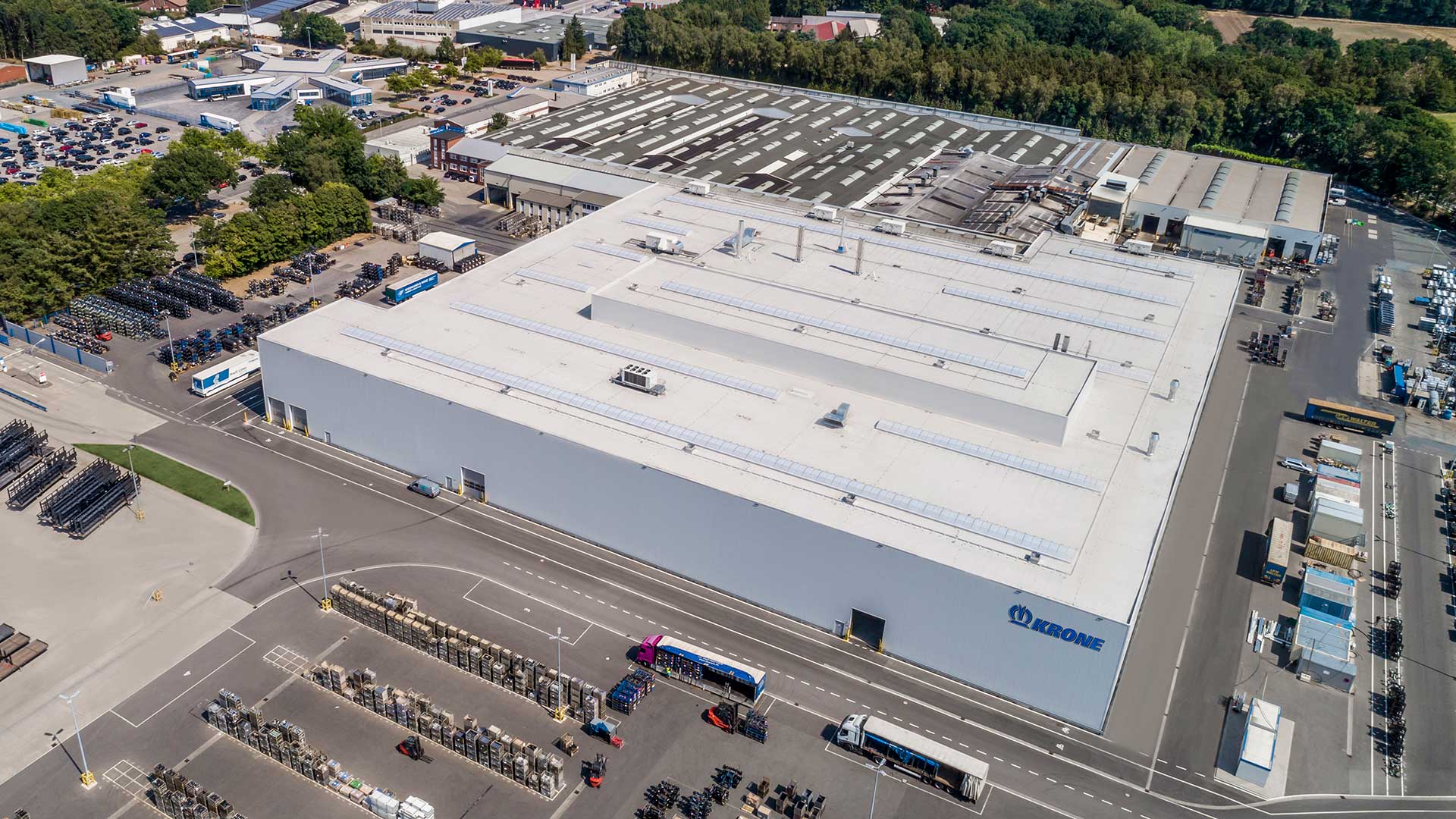
Perfect protection for maximum durability
With its state-of-the-art surface centre in Werlte, KRONE is setting standards in coating technology for commercial vehicles. The centre combines proven cathodic dip coating with powder coating to ensure seamless corrosion protection down to the smallest cavities.
Sustainability plays a key role: thanks to innovative heat recovery and intelligent process control, CO₂ emissions per chassis have been reduced by 40%. The surface centre uses state-of-the-art automation to ensure the highest quality and efficiency. A dynamic, fully automated storage system controls the entire coating process - from blast cleaning and zinc phosphating to individual powder coating in the desired colour.
With an investment of 40 million euros, the surface centre is the largest single investment in KRONE's history. It stands for quality, durability and technological innovation - so that our commercial vehicles remain reliable even under the toughest conditions.
What happens in the surface centre
The chassis blanks are delivered to the surface centre in packs of four and can pass through the delivery lock without having to be shunted. The chassis are stored in the buffer zone until they are transferred to the subsequent production steps. This is where the precise, automated process begins: two indoor cranes and conveyor technology are used to transfer the unfinished chassis to the next station. The warm air from the cooling areas within the coating process ensures that the delivered chassis are warmed up to room temperature and dry before they are processed further.
The first work step takes place in the blasting system: the chassis is targeted with steel balls to remove rolling skin, scale and impurities and create a clean, metallic surface. This is crucial for the adhesion of the subsequent pre-treatment and cathodic dip coating. With 22 turbines arranged three-dimensionally in the blasting chamber, the system achieves optimum results. In the blasting process, steel blasting material is propelled onto the chassis at a speed of up to 300 km/h and fed back into the process after treatment.
The chassis is then pre-treated in the tank line and cathodic dip-paint coated. This involves trication zinc phosphating, which is currently the best and proven technology. The chassis is successively immersed in various tanks in which the baths are circulated around the clock to ensure constant quality. The parameters are continuously monitored.
Once the chassis has passed through the basin line, it enters the cathodic dip coating ovens, where the coating dries at around 190 degrees Celsius. The coating bonds firmly to the surface and reliably protects the component during its subsequent use. After the drying process, the chassis is cooled with outside air and the exhaust air from the ovens is cleaned by a thermal post-combustion system.
The chassis cools passively in the buffer areas, where it awaits the next phase: powder coating. Here, the customer has the option of selecting an individual colour from all RAL colours. Powder coating takes place in one of the two powder booths, with each new colour being prepared by an automatic changeover of the powder system. To ensure maximum efficiency and minimum waste, the colour change is optimised by the automated system. The sequencer, a dynamic and fully automated storage system, ensures that the chassis are fed through the powder booths in the correct order.
In the powder booth, the powder is applied evenly to the chassis. Using a 3D scan grid, the vehicle is precisely measured at the entrance to the booth so that the 47 automatic axles are at the optimum distance from the chassis to ensure an even layer. After this step, the chassis is transported to the second level of the surface centre.
In the powder ovens, the powder coating is liquefied and cured so that it bonds optimally with the cathodic dip coating and adheres permanently to the surface. Once the coating is complete, the chassis is stored in the sequencer until it is called up for assembly. The assembly sequence is defined at the start of the process so that the finished coated chassis is placed in the sequencer in the specified order and then transferred to assembly.